Injection Plastique: Insights into Plastic Injection Molding
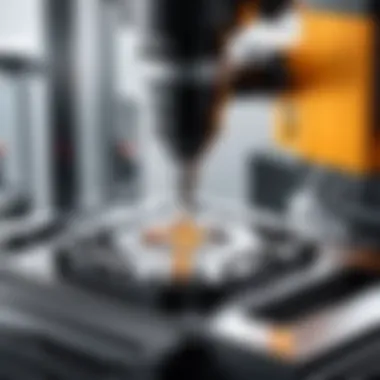
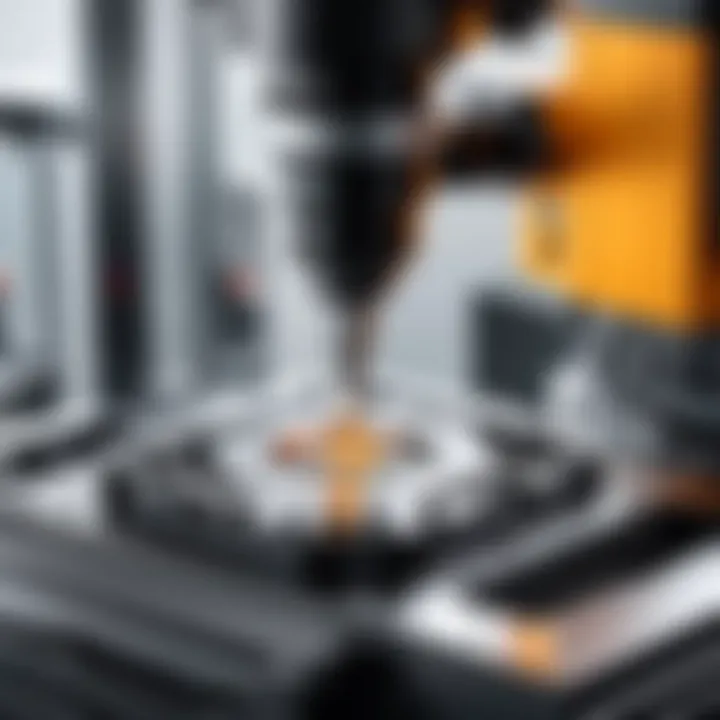
Intro
Injection molding, a cornerstone in the world of manufacturing, is more than just a process to churn out plastic parts. It’s a blend of art and science, involving precision and innovation, and undeniably a driving force in various industries. From automotive components to household items, the implications of injection plastique are diverse and prominent.
In this exploration, we dive deep into the nuts and bolts of plastic injection molding, unearthing the inner workings that define the process. We'll dissect the materials that breathe life into products, and discuss the technological advancements making waves in the sector. With environmental concerns on the rise, this article will also reflect on sustainability matters linked to injection molding.
That said, let's get this ball rolling. We’ll start out by delving into the current technological landscape, dusting off the latest trends and innovations that provide a clear picture of where we're headed.
Technology Insights
In the fast-paced realm of manufacturing, staying ahead of the curve is crucial. Injection plastique is no exception. New technologies are continuously emerging, reshaping the way we think about and execute plastic molding.
Latest Tech Trends
- Smart Manufacturing: Integrating Internet of Things (IoT) devices within injection molding operations allows for real-time monitoring of processes. This leads to increased efficiency and reduced waste.
- 3D Printing Integration: The combination of 3D printing with traditional injection molding is gaining traction. It provides greater design flexibility and rapid prototyping capabilities, especially useful in customized projects.
- Biodegradable Materials: With global environmental issues at the forefront, innovations around bio-based plastics are growing. They’re designed to degrade more efficiently than conventional plastics, aiming for a greener footprint in the industry.
Innovation in Tech
Tech companies are not sitting idle. Many are on a relentless quest to push the boundaries of what’s possible within injection molding. Here are a few noteworthy advancements:
- Energy-efficient Machines: Modern machines are now utilizing advanced hydraulics and electric drives, significantly cutting down energy consumption while improving cycle times.
- Artificial Intelligence: AI is being harnessed to predict maintenance needs and optimize production schedules. This level of intelligence can save significant money and downtime.
- Enhanced Simulation Software: This tech helps designers visualize the molding process before anything is made, minimizing errors and prototype iterations.
"The future of injection plastique lies in the blend of technology and creativity, making manufacturing more sustainable and efficient than ever before."
Product Reviews
When it comes to equipment in the injection molding domain, knowing which products stack up is key. Some notable products include:
- Arburg Allrounder: Renowned for its versatile approach, it offers great flexibility across various applications and is known for durability.
- ENGEL e-victory: This all-electric injection molding machine stands out for its precise control, particularly beneficial in achieving high-quality parts.
- Husky Ultra: A go-to for high-volume production, this system excels in efficiency, often making it the backbone of large manufacturing lines.
Staying informed on the latest trends and innovations not only equips manufacturers with essential knowledge but also influences future strategies. With the next section, we will turn our attention to the environmental considerations associated with injection molding, opening the floor for a discussion on sustainable practices.
Prologue to Injection Plastique
Defining Injection Plastique
Injection plastique refers to the process of injecting molten plastic into a mold to create various shapes and forms. This technique has become indispensable in manufacturing, allowing for the production of intricate and detailed plastic items with a high degree of precision. From small consumer goods to large automotive components, injection molding serves as a backbone in many industries. By shaping how items are made, this method not only enhances efficiency but also promotes sustainability by reducing waste during the production cycle.
The core of injection plastique lies in its ability to mass-produce identical items quickly. The process begins by heating plastic until it liquefies, followed by injecting it into a cooled mold. After cooling, the mold is opened, and the finished product is released. This cycle can be repeated consistently, allowing manufacturers to keep pace with market demands without sacrificing quality.
As technology and materials advance, injection plastique continues evolving, integrating new methods to improve production capabilities and minimize environmental footprints.
Historical Context
The roots of injection plastique can be traced back to the late 19th century. In 1872, a man named John Wesley Hyatt earned a patent for the first injection molding machine. His invention was spurred by the desire to create a material that could replace ivory in billiard balls, giving rise to nitrocellulose plastics—a forerunner to the many variations we see today.
From that point onward, the industry began gaining momentum. By the mid-20th century, innovations in synthetic resins gave birth to a new era of plastic manufacturing. The development of thermoplastics allowed for easier manipulation of materials and the ability to reuse products, setting the stage for modern-day injection molding technologies.
In recent years, the industry has witnessed dramatic advancements, driven by demands for faster production times and cost-efficiency. Organizations have begun adopting automation and smart technologies, transforming injection plastique from a simplistic manufacturing method into a complex, highly efficient production line.
Today's injection plastique not only speaks to the technical mastery behind its process but also reflects societal shifts towards innovation, efficiency, and sustainability—maximizing output while minimizing impact. This evolution is what makes understanding injection plastique so essential, as it highlights the profound relevance of technology in shaping our daily lives and the products we rely on.
The Injection Molding Process
The injection molding process stands as the cornerstone of plastic manufacturing, shaping the way components are designed and produced. As industries search for efficiency, quality, and innovation, understanding the intricacies of this method becomes vital. By shedding light on the components and workflow, one can appreciate why injection molding is not just a technique; it's a transformative process that influences various sectors, from automotive to medical devices.
Overview of the Process
Injection molding is a manufacturing method that involves injecting molten material into a mold to create a solid item. This method is particularly faorble for producing plastic parts that demand precision and uniformity. The entire process starts with material selection and preparation, moving swiftly into melting, injecting, and cooling phases. The effectiveness of this method lies in its ability to produce large quantities of identical parts with minimal waste – a crucial advantage in today's environmentally conscious marketplace.
"Injection molding is like baking a cake where consistency and precision yield the most delightful results."
One of the key benefits of injection molding is its speed. Once the mold is created, parts can be produced quickly, making the system suitable for high-volume production runs. Furthermore, this process reduces the chances of surface defects if the molding conditions are consistently monitored.
Key Components Involved
There are several essential components that make up the injection molding system, each playing a crucial role in achieving high-quality outputs:
- Injection Unit: This part melts and injects the plastic into the mold. It’s responsible for heating the material to its proper viscosity.
- Clamping Unit: It holds the mold in place during the injection process. The pressure and force applied here is key to ensuring proper molding without leakage of the molten plastic.
- Mold: This is the cavity that determines the shape of the final product. Molds can be quite complex, and their precision is pivotal for the accuracy of the produced items.
- Cooling System: After the plastic is injected, it needs to cool down to take the shape of the mold. The effectiveness of the cooling process can significantly affect the cycle time and quality of the final product.
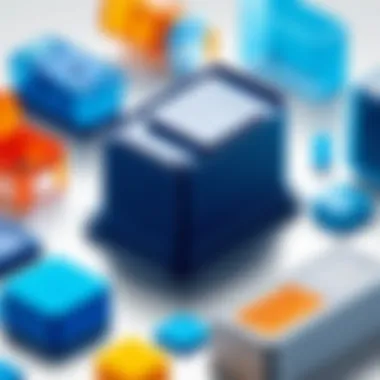
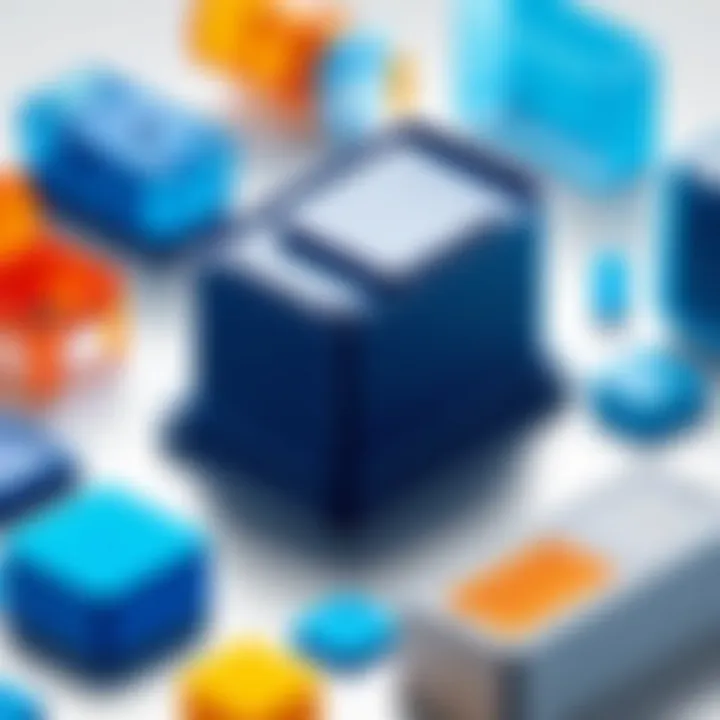
The interplay between these components creates a synchronized workflow that can adjust to various production needs. Having the right balance of these parts often dictates the success rate of any injection molding operation.
Step-by-Step Workflow
The injection molding workflow can be broken down into several clear steps, allowing for a better understanding of how raw materials transform into finished products:
- Material Preparation: Raw plastic pellets are dried and prepped for melting, ensuring that they meet moisture content requirements.
- Melting the Plastic: The prepared pellets are loaded into the injection unit, where heat transforms them into a molten state.
- Injecting into Mold: The molten plastic is then injected into the mold under pressure. This step requires precise control to prevent air pockets that could compromise the part.
- Cooling: The plastic remains in the mold for a calculated period to cool and solidify before removal.
- Ejection: Once cooled, the mold opens, and ejector pins remove the finished part.
- Quality Inspection: The final parts are inspected for defects and dimensional accuracy.
The entire cycle can take anywhere from a few seconds to several minutes, depending on the complexity and size of the part being produced. Optimizing each of these steps enhances overall efficiency and product quality, reflecting the essential nature of the injection molding process in modern manufacturing.
Materials Used in Injection Plastique
The choice of materials in injection plastique plays a crucial role in determining the quality, durability, and functionality of the final product. Understanding these materials lets manufacturers make informed choices, ultimately impacting production efficiency and consumer satisfaction.
Types of Plastics
When it comes to plastics used in injection molding, one can broadly categorize them into thermoplastics and thermosets. Each type has its unique characteristics that make them suitable for different applications.
- Thermoplastics: These materials can be melted and reshaped multiple times without altering their fundamental properties. Polypropylene, polystyrene, and polyvinyl chloride (PVC) are a few examples. They offer great flexibility and are often favored for consumer goods, packaging, and even automotive components.
- Thermosets: Unlike thermoplastics, thermosets harden after being molded and cannot be remelted. Commonly used thermosetting plastics include epoxy resins and phenolics. These materials often provide excellent thermal and chemical resistance, making them ideal for applications like electrical components.
Choosing the right type of plastic is foundational to the success of injection molding projects. Factors like intended use, environmental conditions, and structural integrity come into play.
Additives and Compounds
The mainstay of injection molding is not just the plastic itself, but also the additives and compounds mixed in to enhance certain characteristics. Additives play pivotal roles, significantly influencing properties such as strength, durability, and appearance. Some of the widely used additives are:
- Colorants: These additions impact the visual appeal of the final product. Colorants can be in the form of dyes or pigments. For manufacturers looking to create something visually striking, choosing the right colorant can differentiate a product in a saturated market.
- Stabilizers: Plastics can degrade from exposure to heat, light, and other environmental factors. Stabilizers provide necessary protection, extending a product's lifespan by mitigating degradation.
- Fillers: Fillers like talc or calcium carbonate can bolster strength or lower manufacturing costs by displacing a portion of the main plastic. This is commonly seen in products where structural support isn’t critically reliant on pure plastic properties.
Understanding how these additives work not only aids in enhancing product quality but also in streamlining manufacturing processes. In conversations about sustainability, many companies are now experimenting with bio-based additives, showcasing innovation in materials science.
“Well-selected materials and additives are often the unsung heroes behind the success of injection molded products.”
By closely examining the types of plastics and the additives employed in injection molding, stakeholders can better navigate the complexities of material selection, ultimately leading to improved product performance and competitiveness in today's market.
Applications of Injection Molding
Injection molding is at the forefront of modern manufacturing, playing a crucial role across various sectors. The process is not just pivotal for producing components but also for driving innovation and efficiency within industries. Whether it’s in the realm of everyday products or specialized equipment, injection molding serves a multitude of purposes, making it an integral part of economic activity.
Understanding its applications allows for a deeper appreciation of how injection molding shapes market trends, consumer behavior, and technological advancement. Here we delve into its impact across three major sectors: Consumer Goods, Automotive, and Medical Devices.
Consumer Goods
When it comes to consumer goods, injection molding is like a Swiss Army knife, versatile and reliable. From the humble plastic bottle to sophisticated electronic housings, the ability to produce high-quality parts at scale can’t be overstated. The process allows manufacturers to achieve consistent design, ensuring that every piece meets stringent quality standards. This reliability results in economies of scale, making products more affordable to consumers.
Consider the production of gadgets such as smartphone cases or kitchen utensils. The precise nature of injection molding not only aids in consistency but also opens avenues for intricate designs that cater to modern aesthetic preferences.
- Cost-effectiveness: High-volume production reduces costs.
- Customization: Manufacturers can produce customized designs easily.
- Speed: Fast production times allow for quicker market entry of new products.
Automotive Industry
The automotive industry showcases injection molding's capability to support both mass production and bespoke designs. Cars today are complex assemblies that require precision-engineered components, all of which benefit from this molding process. Parts such as dashboards, battery housings, and numerous decorative elements are molded with high efficiency and remarkable accuracy.
The advancing trend toward electric vehicles has further accelerated the need for lightweight and durable components, where plastics created through injection molding come into play. This not only enhances fuel economy but also meets the growing environmental standards of the industry.
- Material Efficiency: Reduces waste by using exactly the amount needed.
- Weight Reduction: Lighter parts contribute to better fuel efficiency.
- Integrated Designs: Possibility of multi-functional parts reduces assembly time.
Medical Devices
In the realm of medical devices, the stakes are high, and the demand for precision is unparalleled. Injection molding supports the manufacturing of various medical tools, from syringes to complex surgical instruments. The ability to use high-grade, biocompatible materials ensures that products meet the stringent health regulations.
In recent years, there has been a shift towards specialization within this sector, requiring that components be not only functional but also easily manufactured under stringent sterile conditions. Injection molding is capable of addressing these needs, offering consistent quality that healthcare professionals can rely on.
- Sterilization options: Parts can be designed to endure various sterilization processes.
- Precision Engineering: High tolerances for safety and efficacy.
- Innovation: Enables the creation of new devices that can revolutionize patient care.
Injection molding is more than just a production method; it's a key player driving innovation across the consumer, automotive, and medical domains.
Advantages of Injection Plastique
The world of manufacturing is not without its complexities, yet the advantages of injection plastique stand tall amidst the cacophony of methodologies. This section dives into the specific benefits that injection molding brings to the table, outlining why it's often the preferred choice for many industries. The efficiency, precision, and design flexibility associated with this process create a compelling case for its widespread use in various applications.
Production Efficiency
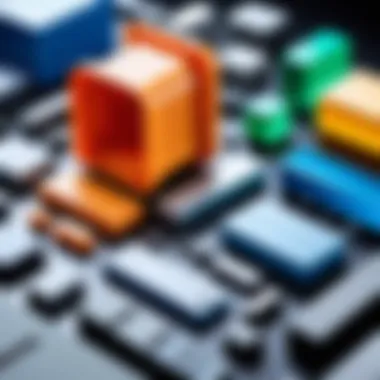
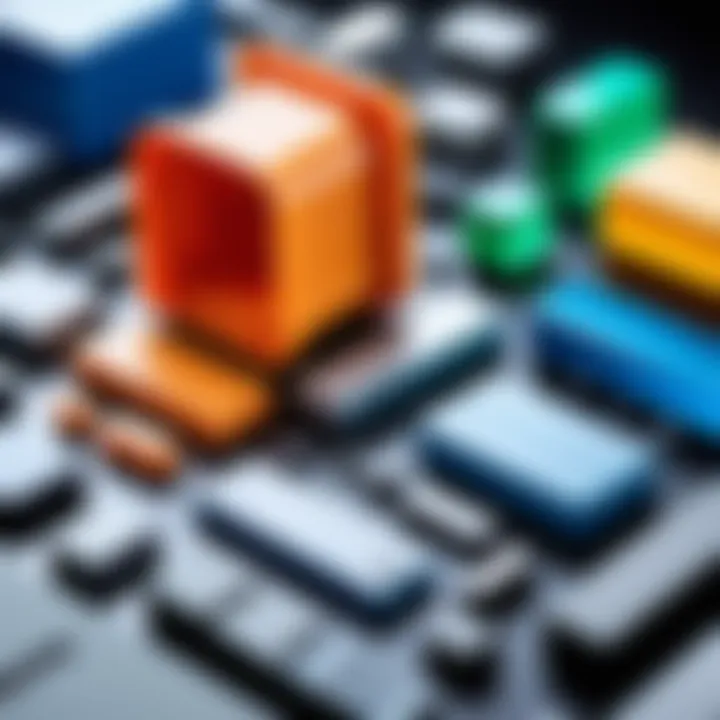
When it comes to production, time is money—this phrase could not be more apt. Injection plastique excels in streamlining manufacturing workflows. Imagine this: a single injection molding machine can produce hundreds, if not thousands, of identical components in a matter of minutes. By minimizing cycle times, companies can ramp up production without breaking a sweat. Its ability to deliver large volumes of plastic parts consistently not only cuts down on labor costs but also improves the overall throughput of the manufacturing process.
In addition to speed, the automation capabilities play a crucial role. Automation reduces human error and guarantees uniformity in the produced items. Furthermore, considering the low wastage rates associated with this process, it's a win-win for manufacturers aiming to maximize resource efficiency. The predictability in production cycles means better planning and inventory management, which ultimately translates into enhanced profitability.
Precision and Quality
In the realm of manufacturing, precision and quality are non-negotiable. Injection plastique is almost synonymous with these principles. The technology employed in injection molding allows for intricate designs and complex geometries, which can be achieved with remarkable accuracy. The journey from design to production can be fraught with unexpected challenges, but injection molding maintains a level of consistency and reliability rarely found in other methods.
It's worth noting that the quality of the parts produced is dictated by the precision of the molds themselves. High-quality molds, coupled with controlled production parameters, ensure that dimensional tolerances are tightly maintained. This results in fewer defects and reduces the need for post-production adjustments, ultimately saving time and resources. Clients in industries—like automotive or medical —demand the utmost quality, and injection molding delivers.
"In the world of precision manufacturing, even the smallest detail counts."
— Anonymous
Design Flexibility
Designers and engineers are often tethered to creativity, and the limitations of traditional manufacturing methods can stifle innovation. Thankfully, injection plastique offers a breath of fresh air in this respect. One of its most significant advantages is the extensive design flexibility it affords.
With injection molding, complex shapes and features can be incorporated into a single part without the need for complex assemblies. This capability allows for more streamlined designs that can reduce part counts, leading to lower assembly costs and improved reliability. Not to mention, materials are available in various colors and textures, providing an extra dimension of customization.
When it comes to quick prototyping, injection molding adapts well. It supports rapid iterations of designs, which are crucial in a fast-paced market where time-to-market is everything. The ability to create molds quickly means that new product concepts can transition from sketches to tangible items faster than one might expect.
In sum, the myriad advantages of injection plastique—production efficiency, precision, and design flexibility—make it a powerhouse in modern manufacturing. As the industry continues to advance, these factors become even more critical in maintaining competitive edges.
Challenges in Injection Molding
Injection molding, despite its numerous advantages, is not without challenges that can complicate production and hinder efficiency. Acknowledging these hurdles is crucial for manufacturers seeking to optimize their processes, ensure consistent quality, and minimize costs. By pinpointing specific issues such as cost considerations, quality control concerns, and the environmental impact, businesses can devise strategies to overcome these obstacles and sustain their competitiveness in a constantly evolving market.
Cost Considerations
The economic landscape surrounding injection molding is intricate. Initial setup costs can be quite steep. The expense starts with the design and fabrication of molds, which can run into thousands of dollars, depending on complexity and precision required. Moreover, the choice of materials can significantly influence costs.
- Material Price Variability: The prices of plastics fluctuate on the market due to factors like oil prices, demand and supply shifts, and international trade dynamics. Selecting cheaper materials can sometimes lead to lower quality products.
- Maintenance and Operation Costs: Machinery upkeep adds to the overall budget. As machines wear and tear, they need regular maintenance, which requires financial investment and can lead to downtime, affecting output.
- Production Quantities: Smaller production runs may not justify the expense of custom molds, leading to decreased profitability. This is where strategizing production numbers against costs becomes essential.
To navigate these financial waters, manufacturers often resort to economies of scale, which can lead to cost savings across large batches. By producing larger quantities, companies can spread the initial costs over more units. Understanding these nuances of cost in injection molding allows businesses to make informed decisions that positively impact their bottom line.
Quality Control Issues
Maintaining quality is a fundamental aspect of production that cannot be taken lightly. When the quality control process falters, it can create a domino effect that results in defective products, dissatisfied customers, and increased waste. In the fast-paced world of injection molding, a few critical factors must be monitored:
- Material Integrity: The materials used must meet specific standards. Any compromise in material quality can lead to flaws in the final product.
- Mold Design and Maintenance: A worn or poorly designed mold can lead to inconsistencies in finished items. Routine checks and recalibrations are essential.
- Operator Training: Skilled operators are vital for ensuring quality. Inadequate training can result in mistakes that might go unnoticed at various stages of production.
Companies can implement robust quality control systems and professional training programs to mitigate these issues. Utilizing advanced technologies for monitoring production can also enhance accuracy and reliability in outputs.
Environmental Impact
As the world shifts toward sustainability, the environmental implications of injection molding are coming under scrutiny. While plastic injection molding has revolutionized manufacturing, creating lightweight and durable products, it brings concerning ecological challenges that need addressing:
- Plastic Waste: The production process generates plastic waste, and if not managed properly, this waste can contribute to environmental pollution. Organizations are increasingly pressured to implement recycling and waste reduction strategies.
- Energy Consumption: Injection molding machines consume significant amounts of energy. As companies endeavor to meet sustainability goals, finding energy-efficient solutions is becoming a priority.
- Sourcing Sustainable Materials: There's a growing demand for biodegradable or recycled materials. Shifting towards these alternatives can be resource-intensive, but it offers long-term environmental benefits.
Manufacturers are encouraged to adopt a green philosophy by exploring recycling options, investing in energy-efficient machinery, and seeking out sustainable materials. By embracing these practices, they can lessen their environmental footprint while still fulfilling market demands.
Advancements in Injection Plastique Technology
The landscape of injection plastique is steadily evolving, and the advancements in technology are playing a significant role in shaping its future. As industries demand greater efficiency and precision, innovations in this field are not just about improving workflows but also about redefining what’s possible in manufacturing. Embracing automation, integrating cutting-edge practices, and adapting to new materials highlight the direction in which injection molding technology is headed. These advancements bring forth specific benefits, challenges, and considerations that industry players must keep in mind.
Automation and Robotics
In recent years, automation has become a cornerstone of modern manufacturing, and injection molding is no exception. The integration of robotics into the injection molding process enhances productivity and reduces error rates. Automated systems, equipped with robotic arms, handle various tasks such as loading materials, unloading finished products, and even monitoring processes—all with remarkable speed and accuracy.
Some benefits of automation in injection plastique include:
- Increased Efficiency: Robots can work non-stop, reducing production times and increasing output.
- Enhanced Precision: Robotics minimizes human error, crucial for achieving the tight tolerances required in complex parts.
- Safety: By letting machines handle hazardous tasks, worker safety is significantly improved.
However, the transition to fully automated systems isn't without challenges. Initial investments are steep, and staff must adapt to new technologies, which can involve training and adjusting workflows. Companies may also face integration challenges with existing systems.
3D Printing Integration
Another fascinating advancement is the integration of 3D printing technologies with traditional injection molding. This hybrid approach allows for rapid prototyping and the creation of complex geometries that may be difficult to achieve using only conventional methods. The flexibility offered by 3D printing enables developers to innovate faster, test designs thoroughly, and only then commit to injection molding for mass production.
Key considerations with 3D printing integration include:
- Design Iteration: Allows for multiple rounds of testing without the need for expensive molds.
- Cost Efficiency: Can significantly lower prototype costs and lead times.
- Material Exploration: Encourages the use of diverse materials, fostering innovation in product development.
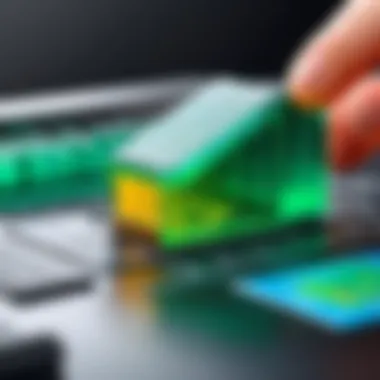
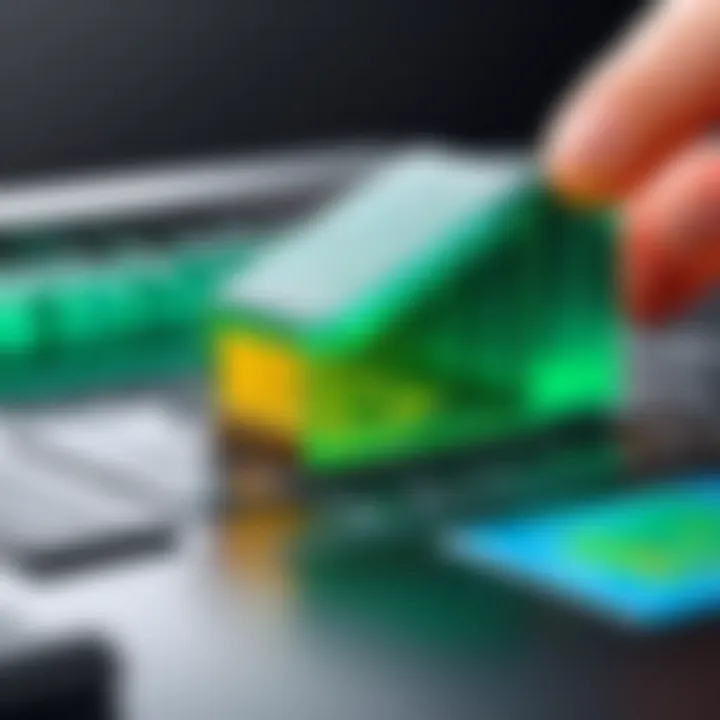
Despite these benefits, there are downsides. For instance, companies might struggle with balancing the production costs of high-quality prototypes against the larger scale efficiencies afforded by traditional molding practices.
Smart Manufacturing Solutions
Adapting smart manufacturing solutions into injection plastique represents a pivotal trend towards more intelligent, data-driven decision-making processes. This involves leveraging the Internet of Things (IoT) and advanced analytics. Smart sensors installed in machines collect real-time data, allowing manufacturers to optimize operations based on analytics insights.
Some advantages of these solutions include:
- Predictive Maintenance: Ensures that machinery is serviced before failures occur, minimizing downtime.
- Operational Transparency: Real-time monitoring allows for quicker response times to production anomalies.
- Resource Management: Enables better tracking of material use and waste, supporting sustainability efforts.
However, the shift towards smart manufacturing does require a cultural change within organizations. Companies need to foster an environment where data is embraced and used actively to improve processes.
"In the race for manufacturing excellence, technology isn’t just a tool; it’s the very engine that drives innovation and efficiency."
In summary, the advancements in injection plastique technology are reshaping the industry significantly. From automation to smart manufacturing integrations, the benefits are substantial but must be navigated wisely. As companies adjust to this rapidly changing environment, the focus should remain not just on staying ahead of the curve but also on leveraging these technologies in a way that aligns with overall business goals.
Sustainability in Injection Plastique
Sustainability in injection plastique has become more than just a buzzword; it reflects a critical shift in the manufacturing world. As the environmental impact of production methods comes under increasing scrutiny, industries must adapt to remain relevant and responsible. This section dives into the urgent need for sustainable practices in injection molding, exploring various strategies and innovations designed to minimize ecological harm while meeting the demands of modern consumers.
Recycling Initiatives
Recycling initiatives play a pivotal role in reducing waste associated with injection molded products. From collection to processing, every stage of the recycling process contributes to a more sustainable approach to this manufacturing technique.
- Closed-loop systems: These systems ensure that discarded plastic products are collected and reprocessed into new items. This reduces the need for virgin materials and lessens the total environmental impact of the plastic lifecycle.
- Collaboration with recycling firms: Many manufacturers have formed partnerships with specialized recycling companies to streamline the recycling process. This collaboration helps in creating efficient systems to deal with production waste and post-consumer products.
- Consumer education: Initiatives often include educating consumers about how to properly recycle plastic items. When consumers understand the recycling processes, it enhances the effectiveness of recycling programs.
Sourcing recycled materials not only conserves resources but also significantly cuts down energy consumption compared to using new resin. Recycling helps keep plastic out of landfills, making it a must-have practice in the realm of injection plastique.
Biodegradable Plastics
Biodegradable plastics represent an exciting frontier in sustainable materials for injection molding. Unlike traditional plastics, which may linger indefinitely in the environment, these alternatives break down more rapidly under specific conditions.
- Material composition: Biodegradable plastics often derive from renewable resources, including corn starch or polylactic acid (PLA). These materials are engineered to decompose, offering a viable alternative to conventional plastics.
- Customizable properties: Manufacturers have increased their ability to tailor the properties of biodegradable plastics to suit various applications. This means they can adapt the material's strength, flexibility, and other characteristics to ensure it meets the requirements of different industries without compromising on performance.
- Environmental benefits: Utilizing biodegradable options significantly diminishes the carbon footprint associated with disposal. When products made from these plastics are discarded, they break down naturally, reducing pollution and landfill overflow.
"Transitioning to biodegradable plastics is not just a trend. It's becoming a necessity in modern manufacturing if we wish to protect our planet for future generations."
Future Trends in Injection Molding
As we look ahead, the landscape of injection molding is poised to undergo significant shifts. These changes are not just a matter of progress; they reflect the industry's ongoing adaptations to technological advancements, market demands, and a heightened emphasis on sustainability. Understanding these future trends is crucial for professionals engaged in manufacturing, design, or supply chain management. By being aware of these developments, stakeholders can better position themselves to utilize emerging tools and practices that enhance productivity and reduce costs.
Market Predictions
Market predictions for injection molding indicate a robust growth trajectory, driven by several factors:
- Technology Integration: The incorporation of advanced technologies like artificial intelligence and machine learning is set to revolutionize production lines. These technologies enhance precision and reduce human error, leading to higher output quality.
- Cost Efficiency: Companies are keen on minimizing operational costs. Innovations in machinery and materials will provide opportunities to achieve greater efficiency without sacrificing quality.
- Customization Demand: As consumers push for more personalized products, manufacturers must adapt to produce smaller batches while maintaining affordability. This flexibility in production will determine which companies thrive in the future.
According to recent analyses, the global injection molding market is predicted to reach a valuation of approximately $300 billion by 2027. This growth signals a robust interest in plastic products across various sectors including automotive, medical, and consumer goods. The trends suggest that companies focused on innovation and sustainability will likely steal the spotlight, leaving those resistant to change behind.
Emerging Markets
Emerging markets present unique opportunities for growth within the injection molding sector. Some of the most promising areas include:
- Asia-Pacific Region: Countries like India and Vietnam are experiencing rapid industrial growth. This region's increasing demand for consumer products and low production costs are attractive to global manufacturers.
- Green Technology Markets: As environmental concerns escalate, there’s a push toward sustainable practices. New markets are opening up for biodegradable plastics and recycling technologies, making them crucial for forward-thinking companies.
- Healthcare Sector: The projected surge in medical device production offers a fertile ground for injection molding technologies. The need for efficient, hygienic, and precise manufacturing processes makes this market particularly lucrative.
- Electronics: With the Internet of Things and smart devices becoming commonplace, the demand for high-quality plastic components tailored for electronics is on the rise. Companies that invest in specialized molds and quick-turnaround production will benefit greatly.
Injection molding is set to evolve rapidly. Those in the industry must pay close attention to trends like automation, environmental impact, and changing consumer expectations.
Overall, keeping an eye on these trends allows businesses to not only survive but thrive in the ever-competitive field of injection molding. Engaging with emerging markets and being adaptable will be key to navigating this changing landscape.
Ending
The significance of injection plastique in today’s manufacturing landscape cannot be overstated. This technique not only fuels innovation across multiple sectors, but it also raises important questions related to sustainability and market dynamics. In this conclusion, we will crystallize the central points discussed throughout this article, illuminating the many facets of plastic injection molding and its ripple effects on various industries.
Summation of Key Points
To sum up, key takeaways include:
- Versatile Applications: Injection molding plays an integral role in producing consumer goods, automotive components, and medical devices. Its adaptability ensures that manufacturers can meet specific design requirements.
- Economic Efficiency: The process is characterized by its efficiency. It allows for mass production with minimal labor costs, thus optimizing overall expenditure.
- Sustainability Initiatives: The industry is moving toward greener practices, such as the introduction of biodegradable materials and recycling efforts, which aim to reduce the environmental footprint.
- Technological Advancements: With innovations like automation and 3D printing, the injection molding process is becoming increasingly sophisticated, thereby enhancing precision and quality.
This comprehensive exploration has helped illuminate the vital role injection plastique plays in modern manufacturing and the continuous evolution it undergoes.
Final Thoughts on the Industry
As we look toward the future, the injection molding industry stands at a crossroads of opportunity and challenge. The synergy between technology and environmental responsibility is paramount. Companies that navigate these waters successfully will not only capture market share but also contribute positively to sustainability. The ongoing trends in automation and the integration of smart manufacturing processes put the industry in a strong position for growth, while a focus on sustainable practices will be essential for long-term viability. Industry leaders must remain agile, adapting to emerging markets and consumer demands with finesse.
"The path forward is not merely about manufacturing more efficiently, but about manufacturing smarter and responsibly."
In closing, recognizing the intricacies of injection plastique is essential for all stakeholders, from manufacturers to consumers. The continued evolution of this sector will define how industries adapt to changing economic landscapes and environmental concerns.